Leaders from Beta Technologies, OnLogic and other companies convened at Generator Makerspace to discuss strategies for recruiting and retaining workers.
In Vermont, there are about two job openings for every unemployed person.
That’s according to Michael Harrington, commissioner of the state Department of Labor, who shared the statistic with an audience of roughly 60 people on a recent Thursday afternoon at Generator Makerspace in Burlington’s South End. The Vermont Manufacturing Extension Center cohosted the event, titled “Advanced Manufacturing Day — Can We Make It?,” at which business leaders gathered to discuss one of the major obstacles facing local manufacturers: Vermont’s labor shortage.
“Unlike other states, our biggest challenge is the number of people in our workforce,” Harrington told the crowd. “How do we attract new people to Vermont, to grow Vermont’s workforce? We’re not going to be able to do it from within.”
Like in America’s Rust Belt, Vermont’s manufacturing sector has declined markedly over the past few decades. An average of 28,500 Vermonters worked in manufacturing in 2023, compared with 46,300 in 2000, according to data from the U.S. Bureau of Labor Statistics.
That drop is despite a proliferation of local tech companies producing everything from electric aircraft to industrial robotics. Across the country, the prevailing narrative about disappearing manufacturing jobs has been displaced by a new challenge: getting American workers back into those hands-on jobs. As both sides of the political aisle look to invest in U.S. manufacturing and the sector has begun to rebound, the domestic workforce has not kept pace.
There will be a projected 2.1 million unfilled manufacturing jobs in the U.S. by 2030, according to a joint study by financial services and consulting company Deloitte and the Manufacturing Institute, a Washington, D.C.-based nonprofit that aims to strengthen America’s manufacturing workforce. The report attributes the shortage to an aging workforce, insufficient job training programs and a general lack of interest in manufacturing careers.
Those problems are amplified in Vermont, the second-least populous state and where more than a third of residents are over the age of 54.
“I personally just get tired of saying, ‘There isn’t anybody. We can’t find anybody,'” Julie LaForce, co-owner of hardwood furniture manufacturer Built by Newport, told the crowd. “I really just try to focus on staying patient, staying really diligent and finding the right folks for our team.”
Tino Rutanhira, cofounder of the Vermont Professionals of Color Network, acknowledged that Vermont’s small population sometimes necessitates employers to search for out-of-state hires. But asking someone to relocate for a job brings new challenges. Vermont employers routinely list the state’s acute shortage of affordable housing at the top of their list of impediments to growth. New, out-of-state hires in particular struggle to find places to live within reasonable driving distance of their jobs.
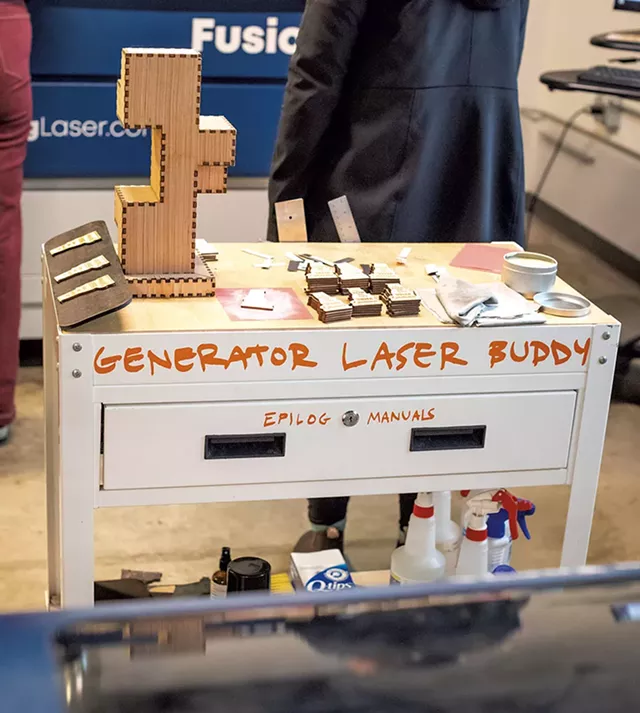
For candidates of color, there may be additional obstacles. “You’re asking them essentially to uproot their family and move them to the third-whitest state in the country,” Rutanhira said. “That’s a harder conversation to have.”
He advertised his Newcomer Nexus program as part of the solution. For $3,000 per job candidate, the network helps companies recruit and retain employees of color from out of state. The organization speaks with applicants during the interview process, then follows up once the workers arrive in Vermont to help them adjust. For example, Rutanhira said, he might suggest a hair braiding salon to a Black woman or connect a Muslim person with the Islamic Society of Vermont.
Kevin Chu, executive director of Vermont Futures Project — which aims to boost the state’s population by 150,000 by 2035 — moderated a discussion in which manufacturing business leaders shared how they navigate hiring. Panelists included LaForce; Diane Abruzzini, cofounder of Rigorous Technology, which makes robots that can do dangerous, repetitive industrial tasks; Kalyn Bixler, director of global manufacturing at OnLogic, which produces industrial computers; and Sarah Deshaw, head of workforce development at electric aircraft pioneer Beta Technologies.
Deshaw emphasized the importance of educating young people about careers in manufacturing.
“A lot of young people know what a plumber is. They know what a carpenter is or an electrician is,” she said. “But when you think about manufacturing, it’s such an incredible variety of roles that you could have under that umbrella. Exposure … is critical.”
Meg Hammond, executive director of Generator, highlighted the makerspace as a place to gain hands-on experience with high-tech manufacturing processes. Celebrating its 10th anniversary this month, Generator provides members with access to 12,000 square feet of workspace equipped with tools such as a 3D printer, a laser cutter and a CNC router. The nonprofit also offers workshops in techniques such as welding, rapid prototyping and computer-aided design.
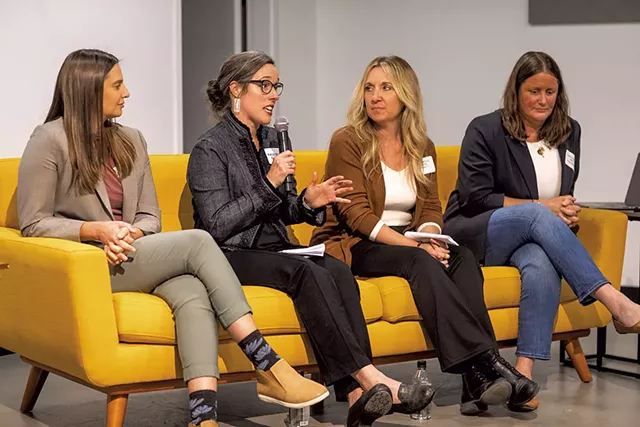
From left: Diane Abruzzini, Kalyn Bixler, Julie LaForce and Sarah Deshaw
After the panel discussion, Generator staff gave tours of the building and demonstrated two tools. The laser cutter carved out a Vermont-shaped magnet, while in the metal shop, attendees donned sunglasses as the plasma cutter crafted a Vermont-shaped bottle opener amid flying sparks.
Hammond announced the creation of a program that will grant young people free membership at the Generator, credit for tool trainings and mentorship from manufacturing companies. She hopes it will benefit unemployed or underemployed 18- to 35-year-olds who “don’t know their path.”
That message resonated with attendee Devon McGarry, a campus recruiter for Husky Technologies, an injection moldings manufacturer in Milton. The company offers an apprenticeship program for high school juniors and seniors. But recruitment is challenging, he said: Students who possess trade skills are hard to come by. That’s a shame, he said, since Husky Technologies’ starting pay for machinists is $23 per hour.
“You can get a fantastic, lifelong career — well paying,” he said. “The job security is pretty darn good without a college degree.”
Illustrative of these challenges: The event at Generator was billed partly as a networking opportunity for job seekers. In an interactive exercise, Hammond asked audience members a question.
“How many in the room are looking for a potential job at a manufacturing company?”
Just three hands went up.
“Wait,” Hammond said. “My facilities director just raised his hand. Sit down, Mason!”
Beta Technologies, OnLogic, Rigorous Technologies and Generator Makerspace will exhibit at the Vermont Tech Jam on Saturday, October 26, 10 a.m. to 3 p.m., at Hula in Burlington. The job fair and tech expo is followed by a keynote presentation with OnLogic cofounder Roland Groeneveld and vice president of HR Lauren Lavallee.
The original print version of this article was headlined “Help Wanted | At Generator Makerspace, Vermont manufacturers trade strategies for addressing the labor shortage”
Read original article here.