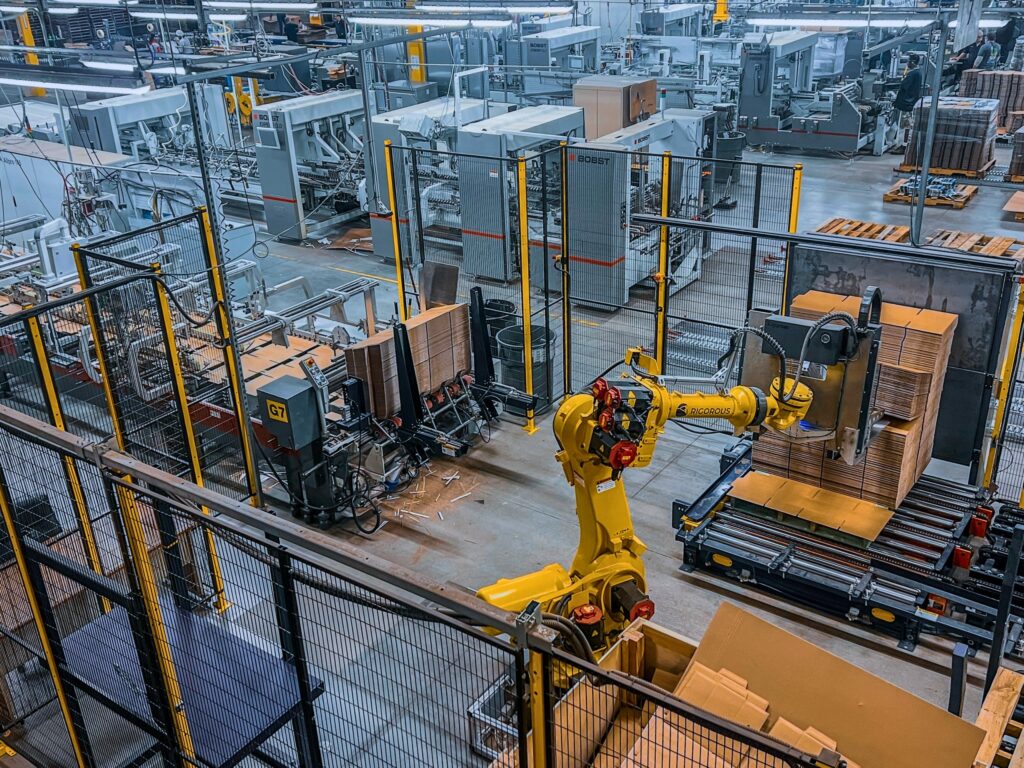
Introduction
A general sentiment in automation is that robotics are flexible to relieve a wide variety of production bottlenecks. Manufacturers have efficiency needs, therefore, robotics are a great solution. Yet, everyone knows that story about the company that installed the robot, found it worked – but didn’t quite work for their operation – and now it’s decommissioned, gathering dust in the corner.
Rigorous was founded to help more manufacturing companies leverage automation to support their business goals without requiring an in-house robotics team. One of our core values is “Be Useful to Humans”. We believe robotics are infinitely more useful to companies when they are purpose-built for a specific application. Turnkey systems are easier to operate and remotely supported by a team of robotics experts.
We work primarily in mature industries that have seen success generation after generation by making incremental improvements with a long-term horizon. Robotics need to work within existing processes, operational requirements, and space constraints, all of which are unique to each client.
Those statements can appear to be at odds: How does a robotics company deliver the value and reliability of an industrial machine while tailoring designs to individual requirements?
Tailored Development Approach
Rigorous products are purpose-built for specific applications. Our Box Hopper prefeeding robot feeds corrugated converting machines, but it will never palletize – you’ll need our palletizer for that. The benefits of purpose-built applications include:
- Intuitive user interface. Operators can easily control the necessary functions of the system through a touchscreen. They can configure new products without entering any code. They can view alarms and diagnostics down to individual sensors.
- Advanced safety features. In addition to complying with standard robotic safety requirements, we take the time to map out every button push in every possible scenario. Our systems run 20+ hours/day, 52 weeks/year; at some point, every button will be accidentally pushed in every scenario. We take the time to map out zones, recovery and homing modes, and dual-check safety barriers to prevent accidents.
- Remote monitoring and support. Rather than writing your robot’s software custom – and only – for you, we have a standard product application with configurable fields that can be tailored to your requirements. By using modular and standardized components, we can rely upon our team – rather than the one individual who wrote the program – to support your system in the field. Gone are the days when you wait for a technician to fly across the country to debug your code. Instead, many of our clients find that their robotic cells work better for them over time, as we can make optimizations from afar as we see how your operators and products work with the machine.
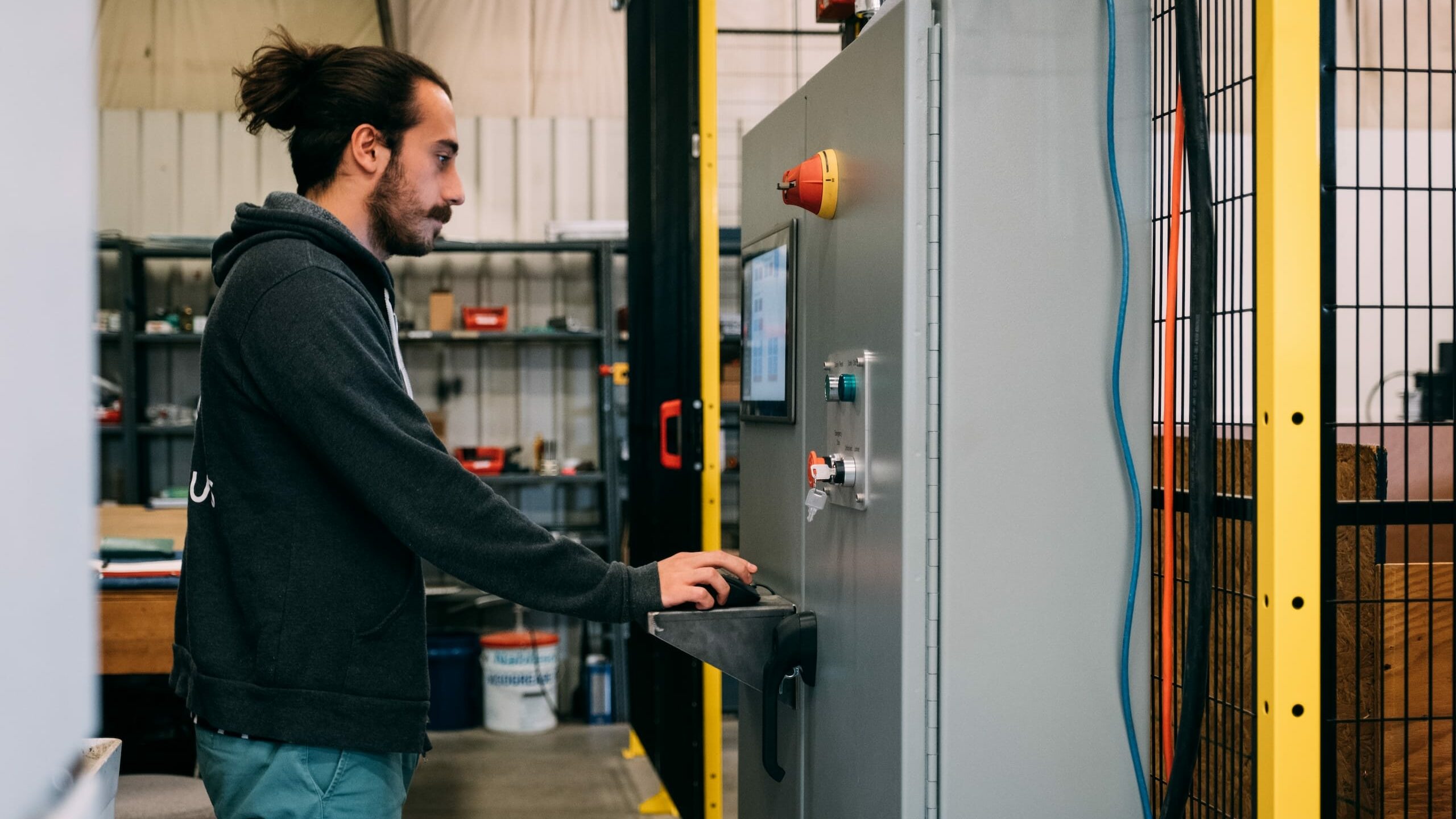
A Rigorous Process
We know that the design doesn’t stop at the proposal stage, we’re just getting started. Rigorous’ roots are in custom research and development programs for novel robotics. Through our team’s experience working on military, government, research, and private industry programs, we have adopted the staged development approach to all of our tailored products.
The Rigorous approach includes three important stages. Design, Development, and Deployment.
Design
While many robotics companies will specify the product during the proposal stage, we recognize that manufacturers often cannot identify their full list of goals, requirements, and constraints before they engage with the robotic cell.
We kick off programs with a Preliminary Design. During this stage, we are focusing on the conceptual process: What are all of the steps required to set up, operate, and shut down the cell?
Deliverables for this stage include preliminary CAD models, robot simulations, layout drawings, system requirements specifications (SRS), and the concept of operations (CONOPS).
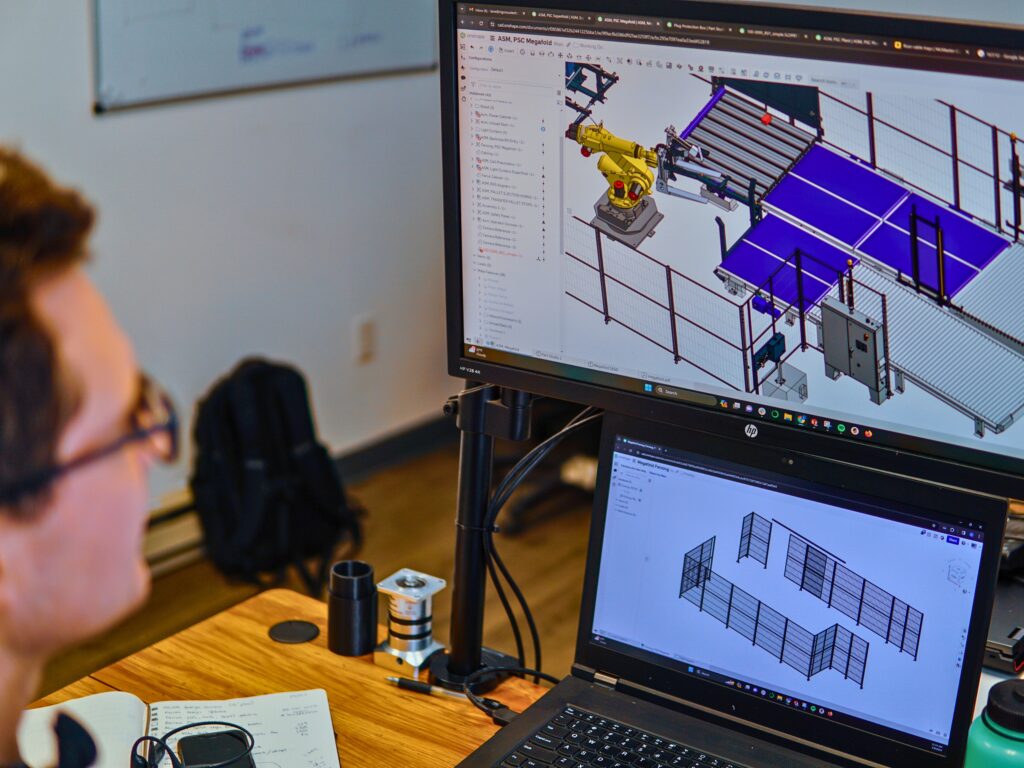
The design stages are opportunities for the client to amend or approve the system designs before we start to cut metal. We present the designs to our customers and hold a collaborative session to solicit input and make decisions.
Once we are aligned with the client on the Preliminary Design, we all understand and agree on how the system will functionally work. That’s when we kick off Critical Designs and do the rigorous engineering.

During the Critical Design phase, we do the mechanical, electrical, and software engineering of your robotic cell. We 3D model any product changes, create robot simulations to ensure we match the reach and speed requirements, map out any software changes, finalize the system requirement specifications (SRS), and tailor the Acceptance Testing to match those requirements. This ensures that your system will be delivered according to your operational needs.
Development
The Development Phase is split into two stages – Build & Functional Testing – and is closed with a successful Factory Acceptance Test (FAT). At the beginning of the Development Phase, we will create a test cell. We will request sample products representative of the types processed. The products will be used to test subsystems and for the FAT.
The test cell will accommodate one full system mockup. The final design will be updated with any modifications found necessary to meet requirements. During the build stage, we will procure off-the-shelf components, fit up the test cell, fabricate custom components, and assemble subsystems. We will begin fitting up the test cell by installing the robotic arm, setting up system power, and building the test fixtures.
We will begin building and fabricating the subsystems for the cell including the vision systems, backstop, EOAT, automatic box prefeed controller, and safety systems. We will wire all electrical components and power on all subsystems. After the initial power-up, we will develop the required control software for all subsystems. This includes conveyor motion, vision systems, robotic arm motions, EOAT motions, and safety functions.
We will conduct functional component testing for all subsystems. We will ensure all subsystems meet the functionality definitions developed during the CDR and confirm the requirements in the SRS are met by each subsystem. This will include fully testing each component individually and testing the system as a whole. Component testing will decouple each subsystem and ensure the mechanical, electrical, and control systems are fully functional. Full system testing will combine all components into the final system and begin system-level testing. We will conduct longer-term testing to ensure system reliability and failure mode testing to ensure easy system recovery during faults.
When the system is fully functional, we will host the NEWW team in Vermont to conduct the Factory Acceptance Test (FAT). Upon successful completion of the FAT, we move on to the Deployment Phase.
Deployment
Our team works with your internal maintenance team or partners to lead installation and integration of the system. After installation, we ramp up your production and tune the machine. After a few days of test production, we move to full-day or half-day production with your team. We train and oversee your operators both with the machine and also with dedicated pieces of training. We close installation with a Site Acceptance Test to verify it functions on your floor as expected.
Once the integration is complete, our partnership continues to grow. We remotely monitor and maintain your robotic cell. Your production data is used to inform decision-making, from software updates to operational recommendations. Our team is dedicated to helping you run your system day after day, year after year. The fact is, our robots work even faster and more efficiently the longer they are in service.
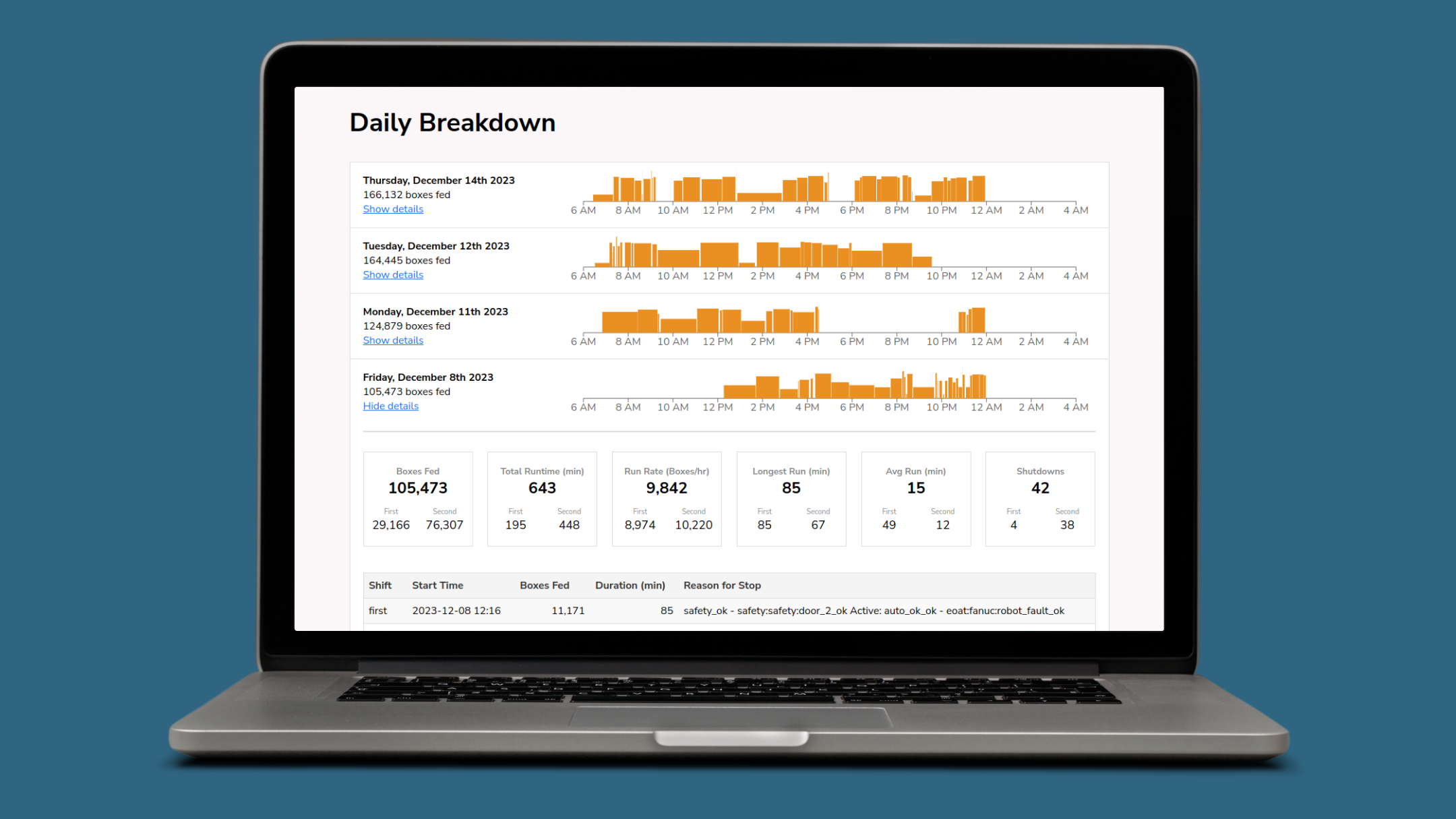
Conclusion
So, how does a robotics company deliver the value and reliability of an industrial machine while tailoring designs to individual requirements?
Rigorous deploys a longstanding and effective process rooted in novel technology development into all of our product specifications. We take the time to do the work, and guide our partners through our program, to ensure that we are meeting your specific operational requirements. We build these designs on the foundation of established and field-tested products and capabilities.